Traduzione da articolo pubblicato su Photovoltaik numero 01/2023, a cura di Sven Ullrich
Test dei moduli ▪ Il Sunlab di Bad Staffelstein dispone di un programma completo per il test dei pannelli solari che ha in portfolio. Qui possono far testare i propri moduli non solo i gestori di grandi impianti e produttori ma sono i benvenuti anche gli operatori di sistemi più piccoli.
Quello che sembra un normale edificio commerciale che sorge all’estremità nord-ovest di Bad Staffelstein in Franconia col suo enorme impianto su tetto in realtà già rivela che si tratta di moduli fotovoltaici. Bisogna premettere che la Sunlab non è specializzata esclusivamente nella distribuzione o produzione. Piuttosto si tratta di un servizio di check up completo del modulo.
Già nel 2009 IBC SOLAR aveva istituito un proprio centro di controllo per offrire non solo ai grandi clienti l’opportunità di far testare i moduli.
Nel frattempo è nato il Sunlab Quality Center, filiale della IBC SOLAR AG di Bad Stafflestein in Franconia: si tratta di un fornitore di servizi per i test sui moduli “Dal momento che gli incentivi vanno ad esaurimento dopo i 20 anni si è deciso di colmare il gap di mercato permettendo anche ai clienti che non hanno accesso ai grandi Laboratori di verifica di far testare i propri moduli”, secondo quanto dichiarato da Florian Spinler, amministratore delegato di Sunlab.
Test anche su piccoli lotti
In effetti soprattutto i gestori di impianti fotovoltaici di piccole e medie dimensioni si sono spesso trovati davanti all’ ostacolo di trovare un laboratorio dove far testare i moduli.
Per quel che riguarda l’offerta di fornitori di servizi bisogna aggiungere che questa è molto selettiva e per lo più si concentra su ordini di grandi dimensioni, anche quando si tratta ad esempio di certificare i produttori o testare la qualità dei moduli forniti per i grandi parchi solari. Questi tipi di certificazioni, del produttore e del prodotto, ci teniamo a specificare che Sunlab le rilascia anche per la casa madre, IBC SOLAR AG.
Il punto forza di Sunlab, che potremmo definire unico, è proprio il collaudo di piccoli lotti: tra i due e 100 moduli si testa tutto.
Valutare il danno del modulo
Accade di frequente che i gestori di impianti solari datati inviino alcuni dei loro moduli a Bad Staffelstein per farli controllare e per verificare che abbiano ancora un livello di efficienza economicamente sostenibile.
Alla fine si tratta di decidere se mantenere in funzione il generatore fino alla scadenza della tariffa incentivante o sostituire i vecchi moduli con quelli nuovi. “ Spesso si tratta però anche di valutare i danni presentati dai moduli. I gestori degli impianti spesso non sono sicuri che i moduli del proprio impianto, dopo una grandinata ad esempio, siano ancora perfettamente funzionanti; ci inviano quindi un campione di cinque, sei moduli” sempre Floran Spinler “ Offriamo inoltre anche un servizio di ritiro dei moduli tramite spedizioniere.”
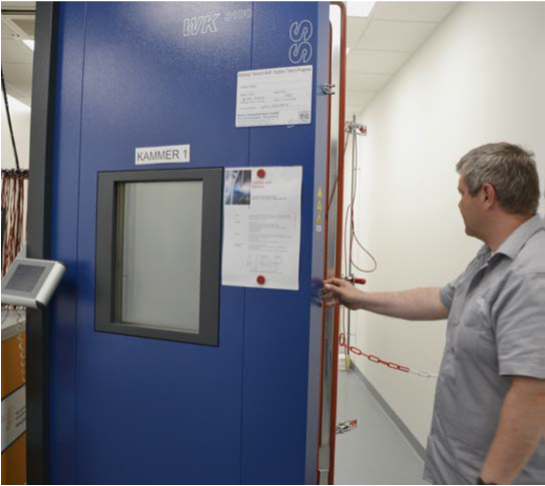
Manutenzione
Nella camera climatica, il Sunlab simula la vita completa del modulo.
In questo contesto possiamo aggiungere che il Sunlab è anche un partner affidabile per le compagnie assicurative. Il Sig. Spinler e il suo collega Markus Pede eseguono infatti anche le misurazioni per le perizie assicurative. “Esaminiamo principalmente denunce con danni da trasporto o danni da incendio, per i quali è richiesto l’intervento delle compagnie di assicurazione”, afferma Spinler.
Verifiche per conto di assicurazione
Le assicurazioni sono state autorizzate a ispezionare i moduli difettosi ed erano presenti anche alle misurazioni. “Abbiamo calibrato e sottoposto a manutenzione i sistemi ogni anno tenendone traccia. Questo ha convinto assicuratori e periti che avrebbero potuto fare affidamento sulla qualità delle nostre misurazioni”, ricorda Florian Spinler. Ecco perché i risultati del Sunlab sono ormai da tempo riconosciuti da assicuratori e periti.
Il Sunlab, ci teniamo a precisarlo, accetta anche ordini più grandi, ad esempio quando si tratta di valutare parchi solari in vendita o misure di garanzia della qualità di forniture per la costruzione di grandi impianti a terra e su tetti. “Quando i moduli arrivano al cantiere, i responsabili del progetto vogliono essere sicuri che non si siano verificati danni durante il trasporto”, afferma il referente di Sunlab, descrivendo l’approccio. “Quindi misuriamo campioni a random. Esiste uno standard internazionale per questo Sistema di campionamento, l’Acceptable Quality Level (AQL), lo stesso utilizzato nell’industria automobilistica.”
La norma definisce la dimensione del lotto
A seconda del numero di moduli previsti per un progetto, viene selezionata e testata una quantità da definire in base alla norma DIN ISO 2859-1 “Dipende dal progetto, questo può essere compreso tra 30 e 3.000 moduli”, afferma Florian Spinler. L’AQL, a sua volta, indica quanto può essere alto il tasso di errore accettabile, in modo che l’intera consegna sia classificata come utilizzabile. Il valore AQL viene concordato tra il fornitore e il progettista. “Noi supportiamo anche il lancio e la certificazione del prodotto”, spiega Spinler.
Ciò vuol dire che il Sunlab può eseguire test su moduli o pannelli appena lanciati da nuovi fornitori. Si tratta di quantità precedentemente definite che devono essere prive di errori prima che la serie di moduli o il fornitore ricevano un certificato corrispondente. In un secondo momento, i moduli passano attraverso tutti i test, che devono essere superati anche da tutti gli altri pannelli che arrivano a Bad Staffelstein.
Si procede con la verifica della potenza massima del modulo in condizioni standard. I moduli in questione vengono pertanto posizionati davanti ad un flasher. Questo simula la luce solare con un dato spettro, un’omogeneità specificata e un irraggiamento di 1.000 watt per metro quadrato.
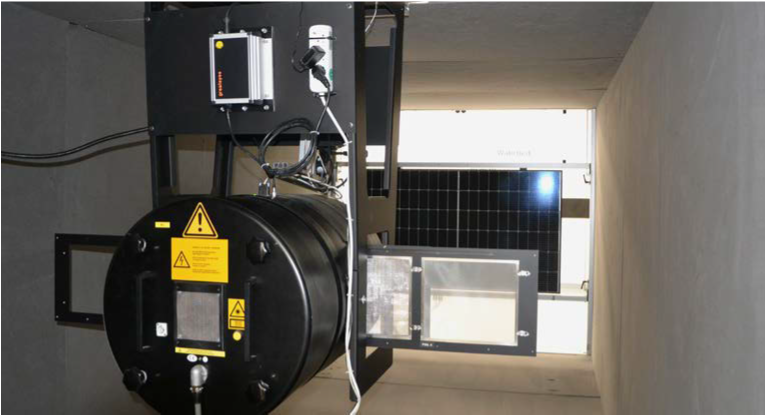
Guardare all’interno del modulo
La temperatura in fase di test deve essere di 25 gradi Celsius e la luce solare simulata deve colpire la superficie del modulo per dieci millisecondi. Esistono anche misure di luce debole, a partire da 100 watt per metro quadrato con incrementi di 100 watt fino ai normali 1.000 watt per metro quadrato.
Con questo tipo di misurazione, gli esperti di Sunlab possono verificare se il modulo raggiunga le prestazioni dichiarate sulla targhetta. E tuttavia anche possibile tenere traccia del degrado annuale e verificare se il modulo sia ancora idoneo per la redditività dell’impianto. In questa fase, gli ispettori acquisiscono anche un’immagine in elettroluminescenza (EL). “Possiamo entrare così a guardare all’interno del modulo fino al livello delle celle e vedere microfessure, fratture o altri difetti che non sono visibili ad occhio nudo”, dichiara Spinler.
Valutare le microfratture
Il difetto viene di seguito valutato sulla base di valori empirici: “Perché, ad esempio, una microfessura non deve necessariamente essere classificata come guasto o danno. Può diventare un problema solo se si acuisce, ad esempio se parti della cella solare vengono poi separate”, Spinler descrive così la procedura. Ciò è rilevante anche quando si valutano danni assicurativi e di trasporto o errori di fabbricazione e installazione. “Se le prestazioni di un modulo rientrano ancora nella garanzia delle prestazioni, ma sono presenti molte micro-crepe sull’immagine EL, il modulo non presenta ancora un difetto. Tuttavia se a causa dei carichi termici e meccanici applicati durante il funzionamento, le microfratture continuano a crescere, il modulo può rompersi completamente dopo due o tre anni”. Sulla base delle specifiche EL, Sunlab è in grado di prevedere tali sviluppi e quindi segnalare i difetti.
Qualità migliorata
In caso di dubbi, invece, è disponibile anche la camera climatica nella stanza accanto al Sunlab, in questa vengono simulati gli influssi meteorologici, non solo per poter comprendere lo sviluppo delle microfessure. “Qui eseguiamo test di temperatura-umidità per 42 giorni a 85 gradi e un’umidità dell’85 percento e test di variazione della temperatura per 25 giorni”, spiega Florian Spinler. Con quest’ultimo, la temperatura nella camera climatica oscilla costantemente tra meno 40 e più 85 gradi Celsius. Con i due test vengono simulate dalle 20 alle 25 vite del modulo. In un secondo momento i moduli, anche se sono sopravvissuti al test come un laminato completo, devono tornare nel flasher e alla camera ad elettroluminescenza. “All’inizio del 2009 in realtà abbiamo inserito interi moduli nella camera climatica e poi li abbiamo estratti di nuovo come singole parti”, ricorda Spinler. “Poiché i fornitori ora sanno che i moduli vengono testati anche in camere climatiche, la qualità risulta notevolmente migliorata. Possiamo infine aggiungere che il test viene ormai superato da gran parte dei moduli.”
Tutto ben isolato
Nelle camere climatiche è possibile rilevare anche il cosiddetto PID del modulo. Questo test viene eseguito a 60 gradi Celsius e con un’umidità dell’85 percento. In queste condizioni, viene applicata un’alta tensione per 96 ore e quindi viene acquisita un’ulteriore immagine EL per vedere se il modulo è suscettibile al PID (Potential Induced Degradation o Degrado Indotto dal Potenziale).
“Ci occupiamo anche della rigenerazione di moduli di impianti in attività” ci tiene a precisare il responsabile del Sunlab. In aggiunta il Sunlab offre la misurazione della resistenza di isolamento, obbligatoria anche dopo il test in camera climatica.
“Aggiungo che con l’invecchiamento dei moduli, possono verificarsi danni all’isolamento, che si manifestano in correnti di dispersione” dichiara sempre Florian Spinler.
A tal fine i moduli vengono immersi in acqua ad una temperatura di 22 gradi Celsius proprio per verificare gli effetti dell’umidità climatica derivante da pioggia, rugiada o neve sciolta.
Si deve evitare che questa umidità raggiunga le parti attive del modulo al fine di escludere corrosione, guasti a terra e rischi per la sicurezza.
Evitare i pericoli
Dopo aver immerso il modulo, il sistema rileva se si verificano correnti di dispersione. A tale scopo viene applicata al modulo una tensione continua di 1.000 volt e viene misurata la resistenza di isolamento. Secondo lo standard, questo non deve essere inferiore a 40 megaohm per metro quadrato di superficie del modulo. Un modulo standard con una superficie di circa 1,6 mq deve quindi avere una resistenza di isolamento di almeno 64 megaohm. Se è più piccolo, il modulo non può più essere utilizzato, in quanto può sicuramente rappresentare un rischio.
Un’altra fase di test importante è il test di carico, Sunlab ha creato una vera e propria tavola di carico. Questa ultima consiste in un’area mobile su cui è costruito un vero e proprio sistema di montaggio per le simulazioni di resistenza dei moduli.
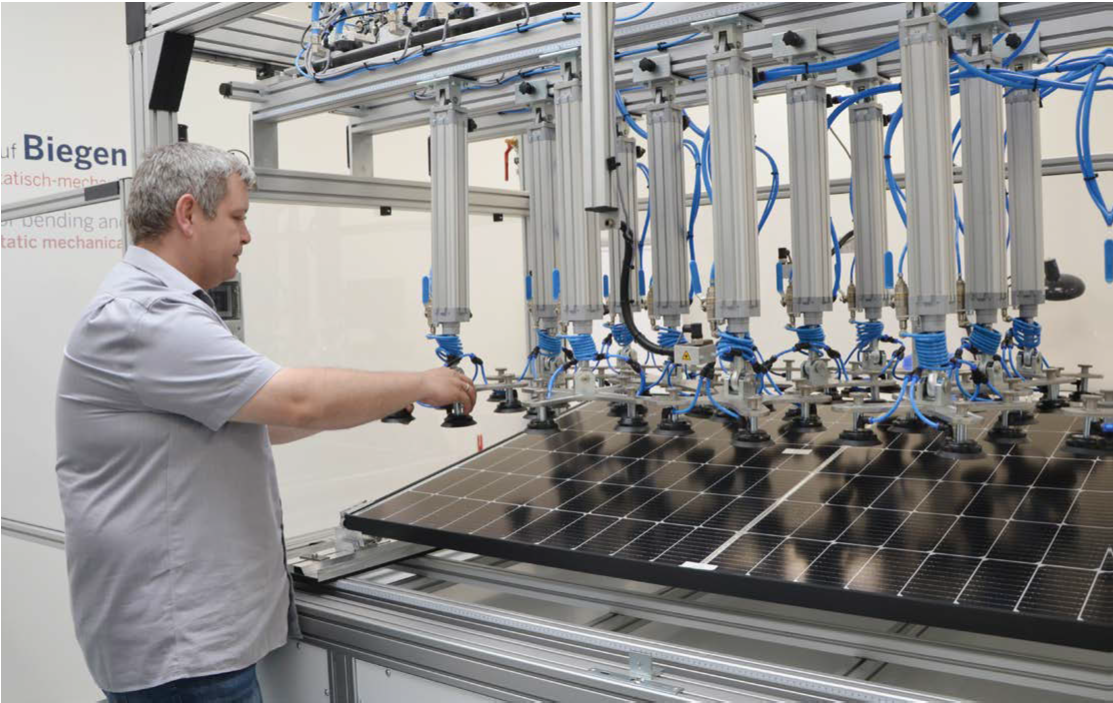
Sotto pressione
In una successiva fase i tecnici che eseguono i test, installano il modulo che deve essere testato.
“Controlliamo sempre le modalità di installazione del modulo e la struttura”, afferma Spinler, spiegando il percorso speciale che il Sunlab ha avviato e precisa “è inutile per il gestore dell’impianto che il modulo e il il sistema di montaggio superino il test separatamente. Se si verifica un danno, non sempre è chiaro quale parte del sistema si sia guastata. Quindi il gestore dell’impianto non sa a chi rivolgersi”.
Una volta che la struttura è stata configurata insieme al modulo, è pronta e funzionante tutto secondo norma. In questo modo, i collaudatori possono vedere non solo se il modulo sta cedendo sotto il troppo carico, ma anche se i morsetti del modulo e la struttura stessa reggono. A tale scopo, i punzoni del piano di carico scendono tutti uniformemente sulla superficie del modulo e premono su di essa con una forza predefinita per un’ora.
Questa procedura viene ripetuta tre volte all’interno di un test.
La forza predefinita deve essere di almeno 2.400 pascal. Sono quasi 245 chilogrammi per metro quadrato. “A seconda delle dimensioni del modulo, anche il peso con cui pressiamo sulla superficie del modulo è compreso tra 700 e 800 chilogrammi”, afferma Spinler. Dopo questo stress test, il modulo torna nel flasher e i tester scattano un’altra foto EL per vedere se il modulo sia in grado di sopportare lo stress meccanico del vento e della neve sul tetto o all’aperto.
1 commento su “Checkup completo dei moduli fotovoltaici”